مشروع صناعة البلاستيك ( الجزء الثالث )
دراسة جدوي مشروع صناعة البلاستيك
الجزء الثالث
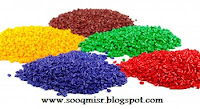 |
مصنع بلاستيك |
اللدائن الرقائقية: LAMINATED PLASTICS
تصنع رقائق البلاستيك بلصق طبقتين أو اكثر من المواد الراتنجية لتكوين وحدة
مفردة أو لوح ذي سمك من البلاستيك. ويعتبر الخشب الرقائقي (بلاي وود) مثال
نموذجي لفهم هذا النوع من الإنتاج حيث تلصق طبقات متعددة من قشرة الخشب
لتكون لوح سميك صلب ، وهو نفس الأسلوب الذي يستخدم في صناعة اللدائن
الرقائقية.
ولا تقتصر المواد الداخلة في عملية التصنيع على البلاستيك فقط
فيمكن أن تكون الطبقات من مواد كالخشب والورق والخيوط مع طبقة من البلاستيك
أو قد تكون جميع الطبقات بلاستيكية بحيث تعطي في المنتج النهائي وحدة
واحدة يصعب فصل طبقاتها.
وتستخدم أساليب مختلفة في عملية لصق الطبقات
ببعضها فأحيانا تستخدم مواد لاصقة قوية وأحيانا أخرى تصهر الطبقات
البلاستيكية مع بعضها وفي طريقة أخرى من طرق صنع الرقائق فان الطبقات
البلاستيكية تشبع براتنج تخليقي والذي يقوم بلصق الطبقات ببعضها ، كما يمكن
استخدام الضغط لأعلى من 1000 رطل / بوصة مربعة لتكوين رقائق تسمى رقائق
الضغط العالي ومن اشهر أمثلتها ألواح الفورمايكا المستخدمة في تغطية أخشاب
المطابخ والطاولات والمقاعد ، أماالرقائق المنتجة بالضغط لأقل من 1000 رطل /
بوصة مربعة فتسمى رقائق الضغط المنخفض ومن أمثلتها بطاقات التعريف.
عملية تصنيع الرقائق The Laminating Process
تستخدم المكابس الهيدروليكية في إنتاج معظم اللدائن الرقائقية ، ويتم ذلك
بتشريب الرقائق البلاستيكية براتنجات مواد الثرموسيتنج (مواد التصلد
بالحرارة) وتترك لتجف ثم ترتب الرقائق فوق بعضها حتى السمك المطلوب ثم توضع
على قاعدة مكبس بين صفيحتين مصقولتين تماما ، وبتأثير الحرارة والضغط
ينتشر الراتنج خلال طبقات المادة مكونا كتلة رقائقية صلبة. وتستخدم راتنجات
الفينولات ، الميلامين ، السيليكون ، الايبوكسي والبوليستر في عمليات
التصنيع وتتراوح درجة حرارة المكبس بين 150 ، 177ºم بينما يختلف الضغط بين
1000 ، 2000 رطل/بوصة مربعة وتستغرق عملية الكبس دقائق معدودة خاصة عند
استخدام راتنجات الثرموسيتنج كما يمكن للعامل الفني اذا اتم الكبس بعناية
ان يرفعها من المكبس وهي ساخنة لتبرد خارجه. أما إذا كانت الراتنجات
المستخدمة من مواد الثرموبلاستيكية فانه يلزم تبريد صفيحة المكبس قبل إزالة
المنتج وذلك بطول دورة التشغيل لضرورة إعادة تسخينها قبل البدء في إنتاج
رقائق أخرى.
منتجات الرقائق Laminated Products
يعتبر ورق الحائط وألواح الفورمايكا اكثر الرقائق إنتاجا واستهلاكا وينتج
الورق المشبع الميلامين ولب ورق الكرافت المشبع بالفينولات وذلك بغمس بكرات
الورق في حوض مملوء براتنج مونمر الفينول السائل حيث يتشرب به حتى التشبع
ثم ترفع منه وتترك لتجف ثم تقطع إلى الحجم المطلوب كبسه ، وفي الورق الخفيف
الوزن الذي يشبع بالميلامين تتبع نفس الخطوات ثم ترص كل الرقائق المطلوبة
مع بعضها وتغطى بلوح شفاف من الميلامين لحمايتها ثم يرص فوقها عدة رقائق من
ورق الكرافت ثم تغطى الرصة بطبقة من ورق الإزالة ثم صفيحة من الصلب
المصقول مع إمكانية وضع عدة رصات داخل المكبس في نفس الوقت ، وبعد فترة
التماسك والتصلب تزال الرقائق وهي ساخنة وتقطع إلى الحجم المطلوب. ويرجع
شيوع استخدام الورق لرخص ثمنه وصلابته وإمكانية الطبع عليه بمختلف الرسومات
والأشكال ، والى جانب ورق الحائط وألواح الفورمايكا تستخدم أيضا خيوط
النسيج كالكانفاه والقطن مع راتنجات الايبوكسي والفينول لتكوين الألواح
الرقائقية ذات العزم العالي مما يجعلها مناسبة للاستخدام في صناعة أجزاء
العزل الكهربي ، صناديق المصهرات (الفيوزات) ، لوحات التوزيع الكهربية ،
وبعض الألواح يمكن تثقيبه أو إخضاعه لعمليات ميكانيكية لإنتاج التروس
والكامات.
الألياف الزجاجية FIBER GLASS
الأساليب المختلفة فى تصنيع الفيبرجلاس:
تستخدم الراتنجات البلاستيكية مع نسيج المادة المقوية في عمليات إنتاج
البلاستيك المقوى ، وعادة تشبع مادة التقوية بالراتنج قبل صبها في القوالب
بعدة طرق فنية مختلفة
حسب نوع المنتج وحجمه ونوع مادة الراتنج والمادة المستخدمة للتقوية.
ويستخدم تعبير الألياف الزجاجية (الفيبرجلاس) غالبا للدلالة على القوالب
المقواة أيا كان نوع المادة المستخدمة في التقوية رغم أن هذا التعبير يشير
إلى الإنتاج الذي تستخدم فيه الألياف الزجاجية في عملية التقوية ، ويبدو أن
ذلك يرجع إلى شيوع استخدام الألياف الزجاجية في معظم المنتجات المقواة
مقارنة بغيرها من مواد التقوية. ومن المنتجات البلاستيكية المقواة هياكل
السيارات ، حشوات الأسطح والجدران ، العصي المستخدمة في رياضة القفز
بالزانة ، مقاطع الطائرات ، خوذات السلامة والقوارب.
الراتنجات المستخدمة في قوالب التقوية
تستخدم راتنجات الثرموستينج أساسا في عملية تقوية اللدائن ، ويعتبر راتج
البوليستر أهم الراتنجات المستخدمة في هذا المجال وذلك لما يتمتع به من قوة
العزم ورخص التكاليف إلى جانب خاصيته في التماسك في درجة حرارة الغرفة
(25ºم) ، ويستخدم في حشوات المباني والقوارب وأجزاء السيارات.
تحذير هام :
يجب ملاحظة أن مادة العامل المنشط أو عامل التصلب المستخدمة عادة لتقوية
الألياف الزجاجية مع راتنجات البوليستر هي مادة غاية في الخطورة ، إذا دخلت
قطرة واحدة من هذه المادة في العين فإنها تسبب تلف نسيج العين بالتالي
العمى إذا لم تغسل بالماء خلال 4 ثوان على الأكثر من وقت الإصابة وإذا لم
يتم ذلك فليس هناك علاج معروف حتى الآن لوقف تلف نسيج العين. والى جانب
البوليسترات راتنجات الداي آليل فيثالات ، السيليكون ، الفينولات ،
الايبوكسي والميلامين اخذين في الاعتبار الخواص المميزة لكلا منها وملاءمة
تلك الخواص للمنتج المطلوب.
مواد التقوية :
كما أسلفنا أن اكثر المواد استخداما في تقوية اللدائن هي الألياف الزجاجية
(الفيبرجلاس) حتى أنها تطلق عليه جميع منتجاته عموما إلا انه يمكن استخدام
خيوط النسيج والبلاستيك والورق والاسبتوس والجرافيت لنفس أغراض التقوية في
حالات خاصة تتطلب احتمال درجات حرارة عالية مع القوة وخواص العزل الجيدة.
أما الألياف الزجاجية فتتوافر على شكل حصائر منسوجة ذات درجات متعددة م
السمك ونوعيات مختلفة من النسيج فقد تنتظم الالياف في جميع الاتجاهات مما
يجعلها سهلة التشكل ف يتجاويف القالب ذات الحدود الضيقة والدقيقة أو قد
تتخذ الألياف اتجاها معينا داخل النسيج يخدم غرض مطلوب في الاستخدام. وهناك
الألياف الزجاجية المفرومة التي تستخدم في القوالب سابقة التجهيز حيث
تختلط مع الراتنج مكونة عجينة يعاد خلطها مع سائل الراتنج ويرش بها سطح
القالب.
قالب البلاستيك المقوى
يستخدم الصلب عادة في صناعة القوالب المغلقة المتوائمة والتي تستخدم في
إنتاج كميات كبيرة من المنتج ويتميز إنتاج هذه القوالب بالأسطح المصقولة من
الجانبين. أما القوالب المفتوحة فتصنع من مواد كالجبس ، البلاستيك ،
الصفائح المعدنية ، الخرسانة والخشب ونلاحظ أن المنتج منها ذو سطح مصقول من
جانب واحد. ويختلف نوع القالب ومادة تصنيعه حسب كمية الإنتاج المطلوب
والتقنية المستخدمة في الإنتاج وكذلك نوع
الراتنج المستخدم. وعادة تثبت هذه القوالب على الصينية العلوية أو السفلية لمكبس هيدرولكي ذي حجم مناسب.
-الإسفنج الصناعي
1- تصنيع الإسفنج الصناعي و أنواعة
يطلب اسم على البلاستيك الرغوي ( وقد يسمى أيضا البلاستيك الخلوي أو
البلاستيك المنتفخ) ويمكن الحصول على هذا النوع بإضافة الهواء أو أي غاز
إلى راتنج البلاستيك لتكوين تلك المادة الإسفنجية.
وقد اعتبرت طرق تصنيع البلاستيك الرغوي أحد التقنيات الرئيسية في صناعة
البلاستيك بعد التطورات السريعة التي شهدتها صناعة قوالب البلاستيك الرغوي
خاصة فيما يتعلق بصناعات التغليف والحفظ والوقاية من الصدمات. ويصنع
البلاستيك الخلوي من راتنجات البوليسترين ، البولي يوريثان ، البولي
ايثيلين ، خلات السليلوز ، الايبوكسي ، السيليكون والفينولات. وتختلف
نوعيات البلاستيك الرغوي حسب نوع الراتنج المستخدم ، التركيب الخلوي ،
الكثافة والجسوءة. وهناك نوعين أساسيين من البلاستيك الرغوي تبعا لخاصية
الجسوء هما :
1- النوع الجاسئ : وهو مقاوم للصدمات بدرجة عالية.
2- النوع
القابل للانثناء : وهو صنف سهل التحطيم ويصنع عادة على اشكال صغيرة الحجم.
ونقصد بالتركيب الخلوي للإسفنج الصناعي هو عدد وحجم الفتحات المتكونة في
رغوة البلاستيك نتيجة مرور الغاز في الراتنج.
2-الرغاوي الخلوية STRUCTURAL FOAMS
تتماثل هذه الطريقة مع عملية حقن الراتنجات الثرموبلاستيكية الصلبة في
قوالب ، ويحصل على الرغوة بإدخال غاز خامل (النتروجين عادة) مباشرة في
الصهير أو يخلط مادة كيميائية تقوم كعامل نفخ مع الراتنج قبل حقنه. ونلاحظ
ان الراتنج الساخن يساعد على انتشار الغاز في الصهير ويدفع الخليط الى
القالب فان الغاز يتمدد مكونا تراكيب خلوية ذات جدار صلب متين. والرغاوي
الخلوية ذات سطح دوامي الشكل مما يجعلها في حاجة الى تلوين للتغطية. ويمكن
إنتاج الأجسام الكبيرة حتى وزن 45 كجم في آلات خاصة مجهزة بمراكم تقوم
بتخزين خليط الراتنج المنصهر وعامل النفخ القادم اليها من الباثق ويحفظ
الخليط في المركم تحت ضغط لمنع التمدد ، وعند امتلاء المركم بالكمية
المطلوبة والمحسوبة من الراتنج يفتح صمام المركم ويدفع الخليط بواسطة كباس
الى تجاويف القالب.
وتستخدم راتنجات البوليسترين والبولي ايثلين لانتاج
الرغاوي الخلوية حيث تستغل في صناعة أكياس القمامة ، إطارات الصور ، أجزاء
الأثاث وبعض منتجات الخشب الحبيبي. أما الراتنجات الهندسية كالبولي كربونات
، ايه بي اس ، البوليستر الثرموبلاستيكي فتستخدم حينما يكون مطلوبا في
المنتج خواص القوة والصلابة السطحية الجيدة كما في المقاعد ، أجزاء هياكل
السيارات ومغلفات الآلات ومعدات المكاتب. وتتميز منتجات قوالب الرغاوي
الخلوية عن منتجات قوالب الحقن العادية أو القوالب المقواة بإمكانية إنتاج
أجسام كبيرة خلال دورات زمنية قصيرة نسبيا كما أن التركيب الخلوي يعطي
قوة إضافية للجسم بالمقارنة مع وزنه مما يمثل خفضا ملموسا في استهلاك
المواد. ويمكن تكسية الأجسام المعدنية متعددة الأجزاء كوحدة واحدة بهذه
العملية والعيب الرئيسي لهذه الطريقة هو الاستثمار الكبير في الآلات .
3-رغاوي الصب
تنتج الرغاوي عامة بخلط الراتنج السائل مع عامل منشط وعامل النفخ الكيميائي
وعندما يأخذ التفاعل الكيميائي مجراه فان الخليط يتمدد مكونا تركيبا خلويا
، ومن الراتنجات المستخدمة في هذه الطريقة عموما راتنجات البولي ايثلين
الرغوية وبلاستيزول كلوريد البولي فينيل.
وتماثل عملية صب الرغاوي عملية صب أي راتنج سائل فيها قالب ذو جزأين مصنوع
من الألومنيوم وله فتحة علوية لاستيعاب التمدد الحاصل في الرغوة المتكونة
ويتم دهان نصفي القالب بمادة مزيلة (ورنيش أو غيره) ويخلط مكونات الراتنج
والعامل المساعد بنسبة صحيحة ثم تصب في النصف الأسفل من القالب ثم يغلق
بسرعة ويربط جيدا بينما يتمدد الراتنج الرغوي لملء تجاويف القالب. ونلاحظ
في هذه الطريقة ندرة استخدام قالب مفتوح في الصب نظرا لعدم حاجتنا إلى ضغط
في تصنيع المنتج كما أن تمدد الراتنج الرغوي فيه يكون بلا ضابط. وتصنع
العاب الأطفال ، أطواق النجاة من الغرق ، الحوامات المائية وشراك البط بهذه
الطريقة. كما تستخدم الراتنجات السائلة المحتوية عوامل منشطة أو عوامل نفخ
كيماوية في عمليات تصنيع الرغاوي المصبوبة فيما يسمى بعملية الصب في
محلــــــــــــــــه (Forming in Place) وتشبه هذه العملية مثيلتها في صب
الراتنجات السائلة إلا أن القالب هنا هو نفس الجسم المراد صب الرغوة
البلاستيكية فيه كأبواب الثلاجات مثلا حيث تتكون رغاوي الراتنج داخل تجاويف
الباب ، والراتنج الأمثل الاستخدام في عمليات الصب في محله هو راتنج
البولي يوريثان في حالتيه المرنة والجاسئة.
ويتم التنفيذ على نطاق تجاري
باستخدام مضخات توزيع تقوم بخلط مكونات البولي يوريثان ثم ضخ الرغوة
الناتجة إلى التجاويف الداخلية لجسم حيث تتمدد ثم تتصلب ، وتزال الأجزاء
الكبيرة يدويا ثم تقطع الزوائد. والى جانب أبواب الثلاجات يمكن إنتاج مقاعد
، الجدران العازلة لبرادات قاطرات السكك الحديدية ، مساند الأذرع وتابلوه
السيارة الأمامي وحجرات الطفو في القوارب. وتتميز طريقة الصب في محله بعدم
حاجتنا إلى قالب للصب كما إنها يسرت إمكانية الحصول على عزل أو تنجيد
للتجاويف الدقيقة في الجسم.
4-الرغاوي المتمددة
يستخدم راتنج البوليسترين كراتنج أساسي في صناعة خرزات التمدد حيث تحتوي كل
خرزة على غاز في تجويفها وعند التسخين فان تمدد الغاز داخلها يسبب بالتالي
تمددها كما ان الجدار الخارجي للبوليسترين ينعم مما يسمح للخرزات أن تنفجر
في النهاية كبالونات صغيرة. وعند وضع كمية كافية من الخرزات داخل قالب
محصور وتعرضت لتاثير حراري فإنها سوف تتمدد لتملأ القالب منتجة ضغطا كافيا
للحام الخرزات مع بعضها مكونـــــــــة رغوة صلبــــــة ذات تركيب خلوي
مغلق ويطلق عليها الرغوة المتمددة (Expanded Foam) .
وتتوافر خرزات
البوليسترين القابلة للتمدد في أحجام قياسية مختلفة حيث تستخدم الخرزات
الكبيرة في إنتاج عبوات التغليف وكتل القوالب بينما تستخدم الخرزات الصغيرة
في صناعة أكواب الشرب. وتصنع قوالب هذه الطريقة من الألومنيوم او الصلب
وتثبت على مكابس تفتح وتغلق حسب دورات التحميل والصهر. والتتابع المثالي في
التصنيع بهذه التقنية هو ملء القالب بالخرزات الجاهزة للتمدد ، تعريض
القالب للحرارة ، التبريد ثم فتحالقالب واخراج المنتج.
ويتم إنتاج الخرزات
الجاهزة للتمدد بتعريض الخرزات إلى بخار ، سخان إشعاعي ، ماء ساخن او فرن
حراري وهذا يصل بالخرزات الى كثافة المنتج النهائي كما يمكن ضبط الكثافة
المطلوبة في الإنتاج التجاري لاعطاء كثافة حتى 20 رطل/بوصة مكعبة. وتنقل
الخرزات سابقة التمدد من وعاء التجهيز ألي القالب إما بتأثير السقوط
بالجاذبية أو بدفع تيار هوائي مضغوط لتملأ القالب تماما ثم يسخن القالب اما
بدفع بخار ساخن مضغوط خلال ثقوب في القالب او داخل القالب جيدا او بوضع
القالب في اوتوكلاف (وعاء ذو بخار ساخن مضغوط) ، وبتسخين القالب نحصل الى
مرحلة التمدد النهائية وانصهار الخرزات ثم يبرد بتيار مائي يمر عبر انابيب
محيطة بالقالب وبرش الماء البارد على القالب المغلق ، ويتم إخراج المنتج من
القالب اما بدفعه من هواء مضغوط او بتجهيز القالب بخوابير للطرد او الواح
انتزاع.
والاستخدام الشائع لمنتجات البوليسترين المصنعة بهذه التقنية يكون
في اغراض العزل او التغليف للأجسام سهلة الكسر ، ويظهر ذلك بوضوع في
البوليسترين القابل للتمدد والذي يأخذ شكل المكرونة الاسباجتي او الدنتيلا
والمستخدم في تغليف الفازات البورسلان او الخزف او الكريستال حيث ان هذه
الخاصية تجعله مناسبا لامتصاص الصدمات.
5-التطبيقات العملية لاستخدام الرغاوي البلاستيكية
نلخص فيما يلي التطبيقات العملية الرئيسية لاستخدامات البلاستيك الرغوي
والتي عرضنا لبعضها أثناء شرحنا لأساليب التصنيع والتي ترجع أساسا الى
خواصه المميزة وهي :
1- الطفو :تعتبر خاصية الطفو للرغاوي البلاستيكية ذات التركيب الخلوي
المغلق ميزة هامة يستفاد منها في صناعة اطواق النجاة من الغرق وعوامات
القوارب والطائرات والشمندورات المستخدمة في ارشاد السفن. وتتميز الاطواق
المصنوعة من الرغاوي البلاستيكية عن مثيلاتها المصنوعة من المطاط بعدم
امكانية ثقبها وذلك نظرا لخاصيتها ذات التركيب الخلوي المغلق الذي يمنع
نفاذ الماء داخله كما انه عادة يكون من البلاستيك ذو النوع الجاسئ.
2-التغليف :ترجع الاستخدامات الكثيرة للبلاستيك الرغوي سواء الجاسئ او
المرن في عمليات التعبئة او التغليف لكثير من المنتجات الغذائية او المعدات
الصناعية او الادوات والاجهزة المنزلية لخواض متعددة اهمها خفة وزنه
وتحمله العالي للصدمات الى جانب سهولة الحصول عليه في اشكال متعددة
وتكوينات مختلفة تلائم شكل وحجم الجسم المراد تعبئته او تغليفه .
3-
التنجيد :حلت الرغاوي البلاستيكية محل كثير من المواد المستخدمة في التنجيد
كالقطن واللباد وغيرها وهذا ما نلمسه بوضوح في مقاعد السيارات والوسائد
ومساند الراس والاذرع والمراتب وصدمات السيارات الامامية والخلفية وكذلك
المشايات .
4- العزل :يستخدم البلاستيك الرغوي ذو التركيب الخلوي المغلق من
النوع الجاسئ في اعمال العزل الحراري لخاصيته المميزة في هذا المجال حيث
نلاحظ ان اكواب القهوة المصنوعة من البوليسترين الرغوي يسهل الامساك بها
دون انتقال حرارة القهوة الى اليد. وتستغل هذه الخاصية في صناعة بطانات
البرادات والفريزرات وصناديق حفظ الاطعمة كمبردات الرحلات وكذلك في حشوات
جدران البنايات وقاطرات نقل المبردات.
5- التركيب :يقصد بالتركيب امكانية
بناء الجسم البلاستيكي الرغوي بمسك يصل الى 6-12 سم ويكون لب هذا التركيب
خلوي الشكل ذو كثافة عالية مما يعطيه قوة عزم تتناسب مع وزن التركيب الناتج
ويتضح ذلك عند استخدامه في صناعة اغلفة الاجهزة الكهربائية المنزلية
والالات المختلفة وكذلك حصائر السفن العملاقة.
زخرفة وتشطيب البلاستيك
تشمل الزخرفة والتشطيب للمنتجات البلاستيكية على عدد لا يحصى من العمليات
والتي يتم فيها دهان ، تغطية ، تلوين المنتج مضيفا اله التصاميم الرائعة
واتليتلفت النظر وتثير انتباه الزبائن حاملة وموصلة للغرض الذي من اجله
صنعت سواء كان المنتج اكياس الحساء او المغلفات المزركشة. وفي صناعة
البلاستيك تتم معظم عمليات الزخرفة والتشطيب اثناء انتاج القالب او بعد صبه
مباشرة وقبل تجميع وتركيب الاجزاء. 1تغطية البلاستيك بالمعدن 2الطلاء
الكهربي 3الختم على الساخن Hot Stamping 4الطبع بالسلك سكرين SILK SCREEN
PRINTING 5الزخرفة داخل القالب IN-MOULD DECORATION 6طلاء اللدائن PAINTING
OF PLASTICS 7الحفر على البلاستيك ENGRAVING PLASTICS
أولا: تغطيه البلاستيك بالمعدن
من التشطيبات المرغوبة لكثير من المنتجات البلاستيكية تغطيتها بطبقة معدنية
رقيقة لامعة وذلك بطريقة تعرف بالمعدنة بالتفريغ (الترسيب المعدني تحت
التفريغ( Vacuum Metallising وفيها يغطى السح البلاستيكي بطبقة من المعدن
يعطيه مظهر معدني براق وجذاب الى جانب ان هذه الطبقة تعطيه مقاومة معقولة
ضد التاكل. ويمكن تغطية معظم انواع البلاستيك بطبقة معدنية بالتفريغ ولكن
اكثر الانواع تطبيقا لهذه العملية راتنجات البوليسترين ، البوليستر ،
البولي كربونات ، الفينولات والايه بي اس مع ملاحظة ان بعض البوليمرات
تحتاج الى معالجة خاصة للسطح قبل تغطيته بالمعدن.ويتطلب انجاز عملية
التغطية بالمعادن سلسلة من الخطوات البسيطة نسبيا تتلخص فيما يلي :-
1- يغمس السطح او يرش بطبقة اساس من اللاكيه (الجملكة) وذلك لتسوية السطح
من أي عيوب غير ظاهرة ولكن تبدو واضحة بعد تغطيته بالمعدن اللامع.
2- يجفف
المنتج داخل فرن.
3- يوضع المنتج على رفد دوار لحمالة نقالي.
4- ويلاحظ ان
الحمالة تحتوي على اسلاك تنجستن خيطية تسخن كهربائيا ومثبت بها قطع صغيرة
من اسلاك الالومنيوم .
5 -توضع الحمالة في غرفة تفريغ ويغلق بابها جيدا ثم
تشغل مضخة تفريغ لسحب اكبر كمية ممكنة من المواد داخل الغرفة.
6- يوصل
التيار الكهربائي الى الحمالة لتسخين خيوط التنجستن والتي تسبب تبخر شرائح
الالومنيوم فيتجه بخار الالومنيوم الى التكثف على السطح البلاستيكي البارد
ويلاحظ ان الرف الموضوع عليه المنتج البلاستيكي يتحرك دائريا حتى يسمح
لبخار الالومنيوم المتكثف بتغطية جميع الاسطح بانتظام.
7- يخرج المنتج بعد
تغطيته بالمعدن ويرش بطبقة حامية من الجملكة نظرا لان السطح الالومنيومي
سهل الخدش. ويبلغ سمك الطبقة المعدنية المغطية للسطح البلاستيكي 5 اجزاء من
المليون في البوصة المربعة مما يجعل الغرض منه زخرفي وليس لمقاومة التاكل
او الوقاية منه. ويمكن تغطية الشرائط البلاستيكية المستخدمة في لف الهدايا
والتغليف بطبقة معدنة وذلك باستخدام بكرات في العملية بديلا عن الارفف
الدوارة.
ثانيا : الطلاء الكهربي
من المعروفان البلاستيك عازل للكهرباء ، لذا فانه يجب معالجة سطحه اولا
بترسيب مادة معدنية عليه ليمكن طلائه بالكهرباء بعد ذلك. وتستخدم معدات
مماثلة تماما للمعدات العادية المستخدمة في الطلاء بالكهرباء العادية ونجد
مميزات عديدة للطلاء الكهربائي المعدني للمواد البلاستيكية حيث يحتفظ
المنتج بالخواص المميزة للبلاستيك مع امكانية استخدامه كبديل للمعدن وهذا
ما نلاحظه بوضوح في الادوات الصحية والاجهزة الصغيرة وكثير من الاجزاء
المعدنية التي يمكن استبدالها ببلاستيك خفيف الوزن مطلي كهربائيا بالمعدن
ليؤدي نفس الغرض الذي تؤديه كما في الادوات المنزلية ، اجزاء السيارات خاصة
الفوانيس الخلفية والشبكة الامامية ومقابض الابواب ولوحات كتابة الاسماء.
وهذه الاجسام جميعها تتميز بخواص البلاستيك من خفة وزن ومقاومة عالية
للتاكل الى جانب مميزات المعدن من بريق لامع وتحمل الاستهلاك الطويل. ويتم
الطلاء الكهربي بالمعادن للمنتجات البلاستيكية تجاريا بطريقتين : الاولى:
استعمال شريط موصل كهربي كالفضة المغمورة في محلول نترات الفضة ثم يغمر
الجسم المراد طلائه في الحوض مع استخدام مصعد كهربي من مادة النحاس فيطلى
الجسم بالنحاس نتيجة فرق الجهد الكهربي ويرفع المصعد النحاس ويستبدل بمصعد
من الكروم او النيكل لتغطيته بطبقة تشطيب نهائي. الثانية: وتشمل غمس الجسم
البلاستيكي في محلول معدني ثم في محلول ملح نحاس او نيكل ثم يطلى كهربائيا
بالكروم او النيكل. وتسمى هذه الطريقة الطلاء الغير كهربي وهي تعطي طلاء
نحاس على سطح الجسم بطريقة اسرع واقل تكلفة من الطريقة الاولى. ومن المواد
البلاستيكية الشائع طلاؤها كهربيا بالمعادن راتنجات البولي كربونات والـ
ايه بي اس ، الاسيتال الفينولات واليوريا.
ثالثا: الختم على الساخن ( (Hot Stamping
رغم قدم استعمال طرق الطبع على الساخن في الزخرفة ووضع العلامات المميزة
على البلاستيك نجد ان التقدم الحديث في معدات الطبع ورقائق الختم على
الساخن جعلها من اكثر عمليات الزخرفة الفنية شيوعا في الصناعة.
واساس عملية
الختم على الساخن هو نقل تصميم او نموذج معين من البوليستر الرقيق او
سنارة من شريط السلوفان (يطلق عليه عادة البطانة) على المنتج البلاستيكي.
ويتم ذلك بتأثير الضغط والحرارة معا على البطانة مما يجعل التصميم يثبت على
البلاستيك وتختلف معدات الختم على الساخن من الوحدات ذات الانتاجية
العالية التي تعمل اليا الى مكابس يدوية بسيطة. وتستعمل ادوات تثبيت مع
قوالب مناسبة في الماكينة تجعل من الممكن الختم على أي سطح بلاستيكي.
وتتكون البطانات المستعملة في عملية الختم من طبقة خاصة مصبوغة او مطلية
بالمعدن على الشريط الحامل ، ويلاحظ ان الصيغ او الطلاء المعدني يجب ان
يكون متوافقا مع البلاستيك المراد طبعه حيث انه سينصهر ويلتصق بسطح
البلاستيك. وينتج صانعي البطانات تركيبات متعددة منها لكل نوع من الراتنجات
البلاستيكية. وتختلف في خواص مقاومة التاكل ومقاومة الكيماويات والالوان.
كذلك يمكن انتاج بطانات خاصة ذات مواصفات معينة.
قوالب الختم على الساخن HOT STAMPING DIES
تصنع القوالب المعدنية المستخدمة في الختم على الساخن عادة من معادن الصلب ،
الماغنسيوم ، النحاس او الزنك. وتستعمل قوالب الزنك والماغنسيوم في عمليات
الحفر على المعادن ذات الاستخدام القصير بينما تستخدم قوالب الصلب والنحاس
في العمليات طويلة المدى وذلك بعد حفرها بالتصميم المطلوب. ويمكن تصنيع
الوالب من راتنج السيليكون وتتميز بمرونتها ورخص تكلفتها مما يجعلها شائعة
الاستعمال حتى في السطوح الغير منتظمة ، وتستخدم كدواسة مسطحة في الختم على
الساخن للحروف البارزة والتصاميم المختلفة والحواشي. وتستخدم القوالب ذات
النسيج المنبسط او على شكل بكرات في الختم المتكرر للتصميم اما الختم على
السطوح الكبيرة المساحة فيمكن استخدام عدة بكرات من السيليكون الساخن كما
في الختم على صندوق التليفزيون. وتصنع حديثا قوالب تجمع مميزات الصلب
والسيليكون وتسمى قوالب ساندوتش ذات خواص مميزة من الصلابة ومقاومة التاكل
والمرونة.
عملية الختم على الساخن HOT STAMPING PROCESS
تشتمل عملية الختم على الساخن وضع الجسم المراد زخرفته في ماكينة الختم
وتثبيته بماسكات وتوضع البطانة المصبوغة باللون المناسب بين الجسم والقالب
الساخن ويفضل استخدام بطانة ملفوفة على بكرة تتقدم بعد كل دورة ختم لتعريض
جزء غير مستعمل تحت القالب وذلك لكسب الوقت وبانزال القالب الساخن لكبس
البطانة على الجسم البلاستيكي لمدة زمنية محددة تنصهر خلالها البطانة فوق
الجسم ناقلة تصميم القالب واللون الذي عليه الى الجسم وبعد رفع القالب يزال
جزء البطانة المستعمل وتكرر الدورة على جسم اخر .... وهكذا. ونفس الطريقة
سواء كانت اليه او يدوية هي المستخدمة في الختم على الساخن امعظم المنتجات
البلاستيكية.
رابعا: الطبع بالسلك سكرين SILK SCREEN PRINTING
تستعمل طريقة الطبع بالسلك سكرين بنجاح تام لزخرفة السطوح السغيرة وكتابة
الاسماء والعناوين معطية انتاج ذو مقاومة عالية للاهتراء ورخيص التكاليف
خاصة في حالات الخطوط الدقيقة والطباعة الفاخرة. وتشمل عملية الطبع بالسلك
سكرين نقل حبر او صبغ خلال ساتر ذو ثقوب دقيقة شبكية الى سطح المنتج
ويستخدم ضغط يدوي او الي لدفع الحبر خلال التصميم الموجود على الساتر. ورغم
ان هذه العملية تسمى بالطبع بواسطة الساتر الحريري الا انه يمكن صناعة
الساتر من المعدن او البلاستيك (خصوصا النايلون.( ويغطى الساتر بطبقة من
الماء او مذيب كيميائي ويستخدم قلم الاستنسل لعمل التصميم المطلوب عليه
ويفضل استخدام الاستنسل التصويري لايضاح الخطوط الدقيقة.
وسواء كان الطبع
يدويا او اليا فان الجسم المراد طبعه يثبت اسفل الساتر بحوالي 3 مم ويضغط
الحبر او الصبغ خلال الساتر فينتقل التصميم الى الجسم الذي يزال ويثبت غيره
لتكرار العملية بينما يجرى تثبيت الحبر او الصبغ على الجسم بتجفيفه داخل
فرن لمدة قصيرة جدا. وهناك عدة انواع من الاحبار والاصباغ تصلح للطبع على
جميع انواع البلاستيك ويساعد علىتثبيتها والتصاقها بالجسم البلاستيكي تاثير
المذيب ، ونلاحظ ان الاحبار التي تثبت اثناء عملية بلمرة تعطي سطح اكثر
جمودة واعلى مقاومة للخدش. وتصمم الات الطبع بالسلك سكرين لملاءمة جميع
اشكال المنتجات البلاستيكية سواء كانت مسطحة او متعرجة او على شكل زجاجات
او شرائط .. الخ.
زرنا على Google+
ليست هناك تعليقات:
إرسال تعليق